Warehousing is a pivotal aspect of retail operations, often dictating the efficiency and profitability of your business. What happens when you run out of space? Expanding might not always be the best option. Whether due to high costs, logistical challenges, or simply the desire to make better use of what you already have, maximizing your existing warehouse space is an excellent strategy. We’ll explore how to maximize your warehouse space without expanding, offering actionable insights that are easy for retail managers to implement.
Why Maximizing Warehouse Space Matters
Making the most of your current warehouse space is more than just a cost-saving measure. It allows you to operate more efficiently, improve your inventory management, and enhance workflow. Retail managers often face fluctuating demands and seasonal spikes, making efficient space use critical for maintaining smooth operations. While it’s important to maximize your warehouse space, it may not be feasible or economical to expand that space with more permanent fixtures. More temporary measures may be necessary.
Assess Your Current Space Utilization
Before implementing any changes, it’s crucial to assess your current space utilization. Conduct a thorough audit to identify areas of wasted space. Look for aisles that are too wide, underused vertical space, and inefficient storage practices. This assessment will provide you with a clear understanding of where you can make improvements.
Employee Input
Your employees usually have firsthand knowledge of inefficiencies. Their input gives you a well-rounded perspective on areas of improvement that might not be immediately obvious through a formal audit.
Benchmarking Performance
Compare your warehouse’s performance against industry benchmarks. This process helps you identify areas of lag and offers a roadmap for optimizing space utilization. Knowing where you stand in relation to competitors can be a powerful motivator for change.
Storage Trailers – Your Efficient Solution
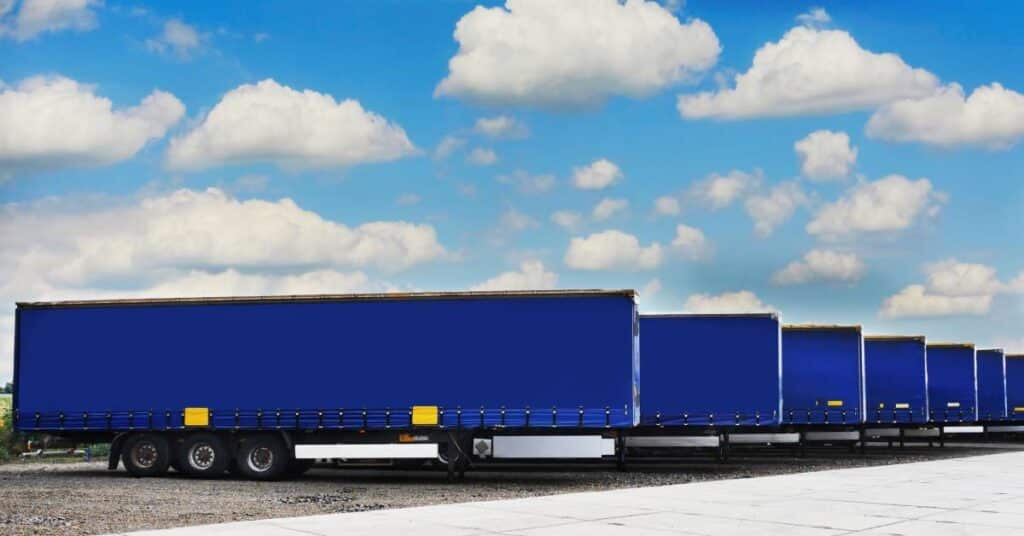
The Growing Need for Extra Space
Warehouses are bursting at the seams, especially during peak seasons. Temporary storage solutions, like storage trailers, can provide the extra space you need without expensive renovations. Leasing a storage trailer provides you with all the space you need without taking up the vast amount of space that a more permanent warehouse upgrade would require.
Cost-Efficiency Matters
While building additional warehouse space is cost-prohibitive, renting or buying storage trailers provides a budget-friendly alternative. This flexibility allows business owners to scale up or down based on demand.
Flexibility and Mobility
Storage trailers offer unparalleled flexibility compared to permanent structures. They are easy to relocate, allowing for adaptive use of warehouse space depending on your needs. The ability to place storage trailers in whatever configuration works best for your space is one of their biggest advantages over costly warehouse expansions that require more room.
Optimize Storage Layout
A well-designed storage layout is the backbone of efficient space utilization. The goal is to maximize every square foot, from floor space to vertical space, while supporting accessibility. These strategies can supplement larger storage strategies, such as leasing storage trailers.
Implement Narrow Aisle Racking
Consider transitioning to narrow aisle racking systems. They reduce aisle width, allowing you to install more racks and increase storage capacity. Forklifts designed for narrow aisles can still operate effectively without compromising accessibility.
Utilize Vertical Space
Don’t just think horizontally—think vertically! Installing taller racks and using mezzanine shelving can increase storage capacity without expanding your warehouse. Many business owners don’t realize how much space they are wasting by not utilizing every inch of their vertical space before they expand.
Dynamic Slotting
Dynamic slotting involves organizing your inventory based on picking frequency. High-demand items should be in easily accessible locations, while less frequently picked items can be further away. This not only maximizes space but also improves pick efficiency.
Adopt Efficient Inventory Management Practices
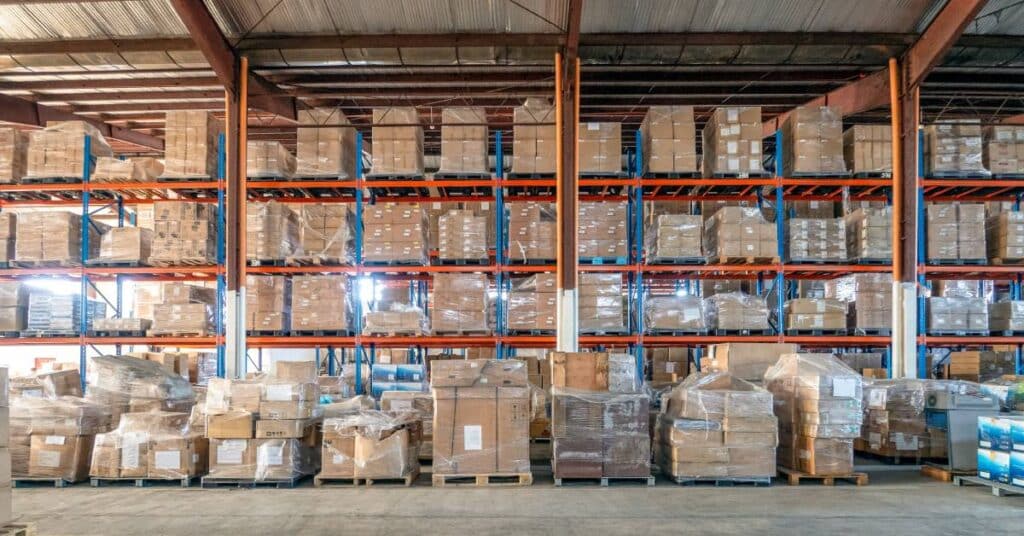
Efficient inventory management is crucial for maximizing warehouse space. Tracking and organization can prevent overstocking and support efficient space usage.
ABC Analysis
ABC analysis helps you prioritize inventory based on value and turnover rate. Classify items into three categories:
- A items are high-value with low turnover.
- B items are moderate in both value and turnover.
- C items are low-value with high turnover.
Focus on optimizing storage for A and B items to maximize space utilization and efficiency.
Just-in-Time Inventory
Just-in-Time (JIT) inventory management minimizes the amount of stock held in the warehouse. By receiving goods only as they are necessary for production or sales, you free up significant storage space. This approach requires precise coordination with suppliers but can greatly enhance space efficiency.
Not all retailers can count on JIT inventory, however, which is where temporary solutions, like leasing storage containers, for excess products can help.
Cycle Counting
Regular cycle counting ensures accuracy for your inventory records. Accurate data helps to maintain optimal stock levels and prevent overstocking and stockouts. This practice supports better space utilization by keeping inventory levels aligned with actual demand.
Continuous Improvement and Monitoring
Space optimization is an ongoing process. Regularly monitoring performance and seeking continuous improvement ensures your warehouse remains efficient and organized.
Key Performance Indicators
Track key performance indicators (KPIs), such as space utilization rate, inventory turnover, and order-picking accuracy. These metrics provide insights into the effectiveness of your space utilization strategies and highlight areas for improvement.
Periodic Reviews
Conduct periodic reviews of your warehouse layout and processes. Regular assessments help in identifying new opportunities for optimization and ensuring your strategies remain effective.
Feedback Mechanism
Establish a feedback mechanism for employees to report inefficiencies and suggest improvements. Encouraging a culture of continuous improvement can lead to innovative solutions and enhanced space utilization.
Maximizing warehouse space without expanding is not only possible but also highly beneficial. By assessing your current space utilization, adopting efficient inventory management practices, and leveraging temporary warehousing solutions like storage containers, you can transform your warehouse into a well-oiled machine. For retail and warehouse managers, these strategies help to save costs and improve efficiency and customer satisfaction.
Trailer Leasing Solutions LLC is your go-to source for dry van trailer leasing in Fort Worth, TX. We can help you address your warehousing needs as soon as possible without expanding your space in an unsustainable way.